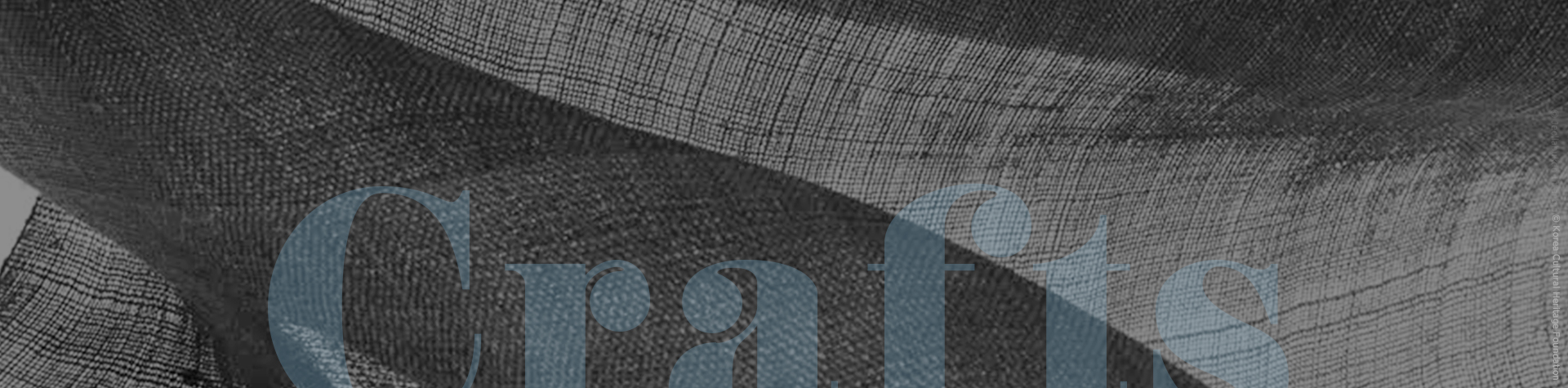
You can¡¯t make an outfit without textiles. Nowadays, we have advanced technologies
and materials flooding the market with a wide array of textiles. However, traditional textiles were made of animal and plant materials, making them rare and prized products. Of such traditional textiles, those woven by human hands, thread by thread, were the ultimate in human labor. Regardless of the development of new technologies, mosi, or fine ramie fabric, is still made by hand. It is a cultural heritage item of humanity woven from the sweat and tears of its creators.Written by Lee Eun-yi , Designer & Writer
¡°Tearing the flesh and drawing blood on the loom all through the short nights of May and June. Could I buy a rice paddy or field? When one roll of cloth is finished, the cock crows and dawn breaks. How can the mosi be so fair and white when it¡¯s been drawn from my own blood? Getting up from the loom to stretch, I find myself already greyed.¡± These lyrics are from a song sung by mosi weavers. It tells of the hard labor involved in weaving mosi. A roll of mosi, roughly 31 cm wide and 21 m long, can only be obtained through an arduous and time consuming process.
First, the fine ramie is harvested and the outer husk is removed. Then, the inner layer is soaked in water and dried repeatedly. Using their own teeth, the weavers break down the inner husk to draw out the strings, connecting the fibers by hand. This thread is then treated with soybean glue to smooth the joints. The thread is fed into a loom in longitudinal and latitudinal directions, finally to be woven into mosi. The entire process takes almost two months. Although fine ramie textiles have been produced in China, Japan, India and elsewhere, Korean mosi has always had a better reputation. Hansanmyeon in Seocheon, Chungcheongnam-do Province, is a key region in the production of mosi, with the weaving of mosi in the Hansan region having been put onto the UNESCO list of intangible cultural heritage items of humanity in 2011.
The weaving of mosi dates back to the Three Kingdoms Period of Korea (57 B.C.-A.D. 668), and the textile has been used to make summer clothing and underwear ever since then thanks to its outstanding breathability and durability. The rough texture does not stick to the body. The textile is lightweight, efficiently absorbs perspiration and dries rapidly. It also does not irritate the skin, being made of natural fibers. As it is washed multiple times over the years, it gets whiter and takes on a luxurious sheen. Clothing made of mosi used to be so highly prized that it was passed down across generations and used as funeral shrouds. Women made sure not to waste any of this fabric, using the scraps to make tablecloths, screens and patchwork.
Although the cool textile is ideal for summer, mosi is a demanding material, being costly, easily wrinkled and prone to splitting. However, one textile manufacturer has recently developed a method to mix rayon and cotton with mosi to enhance its functionality, while using modern manufacturing techniques to allow mass production. This modern mosi is now widely used in clothing and socks. One manufacturer of screens has launched a product made of mosi, taking advantage of its insect-proof properties and breathability. Mosi is also used in accessories such as lampshades and wallets to incorporate a traditional sensibility. Precious mosi, once the product of perseverance and painstaking labor, is becoming a familiar part of our daily lives through such efforts.